Examining the Functional Differences of Robot Transfer Units and Cobot Transfer Units
In season 2, we introduced Morrell Industrial’s engineered linear modules, a pre-engineered linear movement system capable of heavy loads and high speeds. We explored how these modules are pivotal in moving robot transfer units (RTUs). RTUs are more than an extension of a robot’s working range; they’re a fundamental component in modern automation, vital for handling substantial workloads in large-scale production. But in today’s industrial manufacturing world, the RTU isn’t the only player in the field. Though similar, the collaborative robot transfer unit, or cobot transfer unit (CTU), allows manufacturers to undertake the same tasks as RTUs but on a safer, smaller, and more economical scale.
In this episode, host Tim Wilson is joined by special guests Tom Rinke, Advanced Engineering Manager, and Jim Dougherty, Mechanical Product Manager, to discuss the fundamental and functional similarities and differences between RTUs and CTUs. Tom explains that an RTU is an application-based module for industrial robots, usually boasting a large scale, long travel, high loads, and high speeds. They’re typically not made by the manufacturers that utilize them; however, the robots are programmed and controlled by the manufacturer’s own code. CTUs operate very similarly. They’re also application-based modules, but they’re smaller, more lightweight, and, most importantly, safe for humans to work alongside.
Though RTUs and CTUs are fundamentally similar, their functions are where they start to differ. RTUs will go where commanded at full speed and capabilities, regardless of what may be in their way. CTUs, though, with appropriate safety functions in place, continuously monitor force feedback, and if they encounter an obstacle or resistance, that resistance will trigger a stop – this significant difference in function results in CTUs being safer for humans to work with or nearby.
Because the robots used on RTUs and CTUs are different, both types of transfer units are not designed to the exact specifications and the same levels. On CTUs, the guidance system does not need to be as big or heavy because the loads are lower. The small payload also means CTUs will not need to be capable of the same speeds as RTUs. Among other differentiators is the drive system of the transfer unit. RTUs are primarily rack and pinion driven for their precision, accuracy, load-bearing capabilities, and travel distance. CTUs, on the other hand, function optimally with a gear rack system, as cobots are more lightweight, generally have smaller payloads, and don’t need to travel as far distances.
Though RTUs have been used for quite some time, and CTUs have been in the mix for about ten years now, the adoption and integration of both RTUs and CTUs will only grow. As people become more familiar with these systems and discover what does and doesn’t work for each type of transfer unit, CTUs will become more prevalent in industrial manufacturing and automation systems.
To stay up-to-date on Morrell Industrial’s involvement in the development of CTUs, including our own CTU line, follow us on LinkedIn.
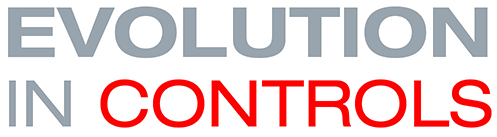