Explore the Automated Tightening, Rivet Mashing, and Lubrication Systems
Every time you go out for a drive, it’s almost certain that you’ll encounter a semi-trailer; they’re everywhere. We rely on them to get goods and materials from point A to point B, and as vehicles that literally carry our economy, it’s essential that the trailers are durable and reliable. However, as vehicles we encounter in large numbers on our highways, we need them to be safe. If our lives depend on them to be of high quality and security, then the manufacturers of these semi-trailers can have no lesser standard. In this episode of Evolution in Controls, special guests and product managers Jim Ross, Ryan Zentz, and Dale Johnston present and discuss three highly innovative and automated solutions for trailer manufacturing that help to ensure safety, reliability, and quality.
Tightening
When building semi-trailers, the lug nuts that tighten the wheels into place must be torqued to the correct amount. As a manual process, it’s not possible to measure or track the actual amount of torque on each lug nut. This lack of consistency can lead to lug nuts being under or over-tightened, which presents safety and quality hazards. Without traceability and accuracy, there’s no way to ensure safety and reliability.
Jim introduces us to the Automated Tightening System, a system designed to accurately torque wheel lug nuts to the correct specs every time. This system features a wheel multi-tool with five spindles. Each spindle engages onto the respective lug nuts at the same time, and when a worker pulls the trigger on the wheel multi-tool, every lug nut is tightened simultaneously to a pre-torque and a final torque. The multi-channel controller included in the Automated Tightening System monitors feedback from start to finish and sends that info to an internal database, becoming part of the manufacturing record. Data tracking and management help to monitor quality and provide a means of traceability should an issue occur post-manufacturing.
Riveting
Another area of trailer manufacturing that significantly benefits from a new innovative automation solution is riveting mashing. As a manual process, workplace safety hazards are present, and energy costs are higher than necessary. Rivet mashing processes utilize hydraulic power units that power the systems that mash the rivets into place, requiring long hosing that is strung across the workplace floor. In addition, different tools are needed for hole punching and rivet mashing.
Ryan walks us through the Automated Riveting System, which utilizes Sytronix, a servo-powered hydraulic power unit that utilizes flow command with pressure override for better control over the entire process. Sytronix units are smaller than traditional HPUs, allowing the Automated Riveting System to be contained within a single rolling cart. This removes the hazard of long hoses strung across the floor while improving the system’s mobility and efficiency. Sytronix units also significantly decrease energy usage as the system smartly adjusts the pump’s drive, reducing speed or pausing to save energy. With Sytronix, the Automated Riveting System provides highly precise, repeatable rivet mashing for semi-trailers.
Lubrication
Finally, lubrication can also have a significant impact on the safety and reliability of semi-trailers. As a manual process, several issues arise, including workplace hazards such as spilled fluid, unnecessary waste, and premature wearing of components. Additionally, it can be difficult to know how much lubricant is the proper amount, and there’s always a risk of accidentally using the incorrect lubricant.
As a solution to these numerous challenges, Dale explains the Automated Lubrication System. This system automates the lubrication process to help eliminate human error when it comes to picking, preparing, and dispensing lubrication. All the worker needs to do is scan a bar code, wait for the system to select and prepare the correct lubricant, and align the hose to plug into the axle. From there, the system automatically dispenses the proper amount of lubricant. In fact, the worker could even walk away during the lubrication – that’s how reliable this system is.
Like the Automated Tightening System, this system provides traceability by tracking all system info and storing it in an internal database. With the Automated Lubrication System, no more residual fluid is wasted in the bottom of the containers, and worker safety is improved with no fluid spillage.
Stay up-to-date with our automated trailer manufacturing solutions and be the first to know of other exciting motion control solutions by following our LinkedIn profiles: Morrell Group and Womack Machine Supply.
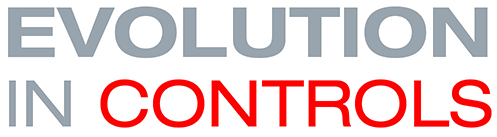