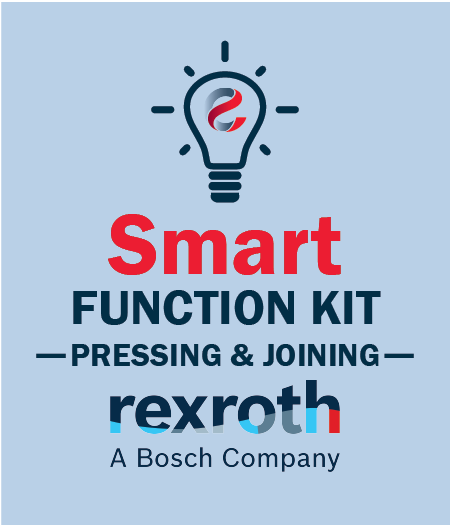
Plug & Produce with the New Smart Press Kit
With the new Smart Function Kit for Pressing and Joining, Bosch Rexroth delivers – for the very first time – a ready-to-use system of proven Rexroth components for joining processes, including an easy, web-based software solution.
The Smart Function Kit for Pressing and Joining consists of perfectly matching hardware and software components. It can be used either as a standalone solution or integrated in higher-level systems via fieldbus.
Call 248-373-1600 to schedule a live demo, or email us
One System Solution, Many Benefits
Easy Product Selection
- Preselected mechanical, electrical and software components from Bosch Rexroth are combined in various kits for forces from 2 to 30 kN
Plug & Produce
- Delivered in a single package, including preinstalled operating software
- Auto parameterization of the servo drive
- Small number of interfaces (servo drive with integrated motion control)
Zero Programming
- No programming knowledge required
- Easy and logical configuration of the process and the evaluation elements
- Browser-based web HMI can be used on various devices
- Modern and intuitive design
Smart Press Kit Infographic

Mounting and Joining Applications
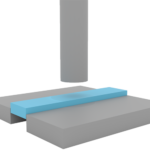
Press Fitting
Examples: Stator packages for electric motors
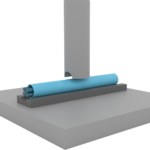
Crimping
Examples: Hoses, cables and plastic parts
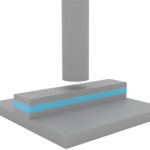
Pressing
Examples: Sintering or powder press applications
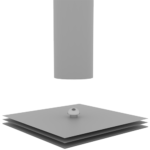
Riveting
Example: Economical joining of sheet metal parts
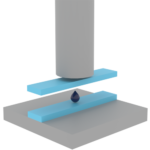
Bonding
Examples: Bonding of plastic and composite materials
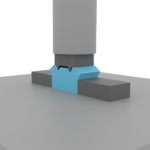
Caulking
Examples: Integration of magnets in lamination stacks
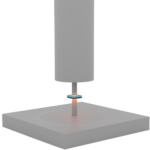
Welding
Examples: Hot plate welding
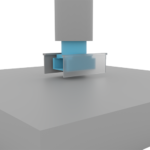
Clipping
Example: Connector contacts in connector housing
Forming Applications
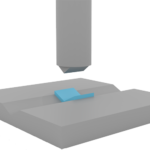
Bending
Examples: Pipes in the metal industry
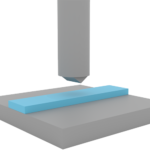
Embossing
Examples: Logos in plastic film
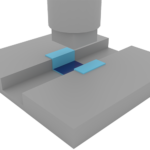
Deep Drawing
Examples: Production of packaging
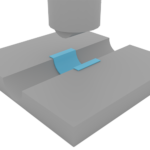
Shaping
Example: Boxes in the packaging industry
Testing Applications
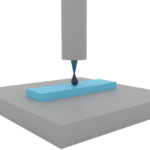
Measurement
Examples: Test stands
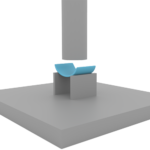
Testing
Examples: Test setups for dampers, springs, brake pedals
Intuitive Software
Commissioning with Auto Configuration (Plug & Produce)
- Preinstalled software
- Wizard for fast, easy commissioning
- Automatic loading of hardware configuration
- Auto parameterization of the servo drive
- Support for commissioning with homing and jog mode
Benefits
- Time savings thanks to Plug & Produce
- Fewer errors and increased productivity
- Significantly reduced complexity
Simple Programming and Operation
- Modular process configuration with drag and drop
- Logic check of input data
- Easy graphical creation o evaluation and analysis elements
- Visualization of process and status information in the dashboard
Benefits
- High level of user-friendliness – no programming knowledge required
- Error reduction and avoidance
Analysis and Diagnosis via Dashboard
- Analysis of force-displacement curves
- Visualization of the process result (OK/NOK)
- Storing of process data for quality assurance in an internal database
- Press history with filter and export function
- Diagnostic functions: system parameters as well as status reports and statistics
- Log book with plain text error messages integrated in the software
- Data access via ReST programming interface
Benefits
- Always up-to-date with current process data such as position, force and speed
- Short reaction times in case of deviation
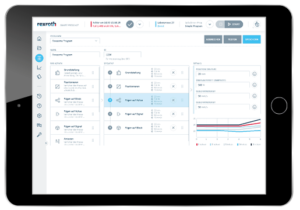
Kit Specifications
Size | SPK 002 | SPK 004 | SPK 007 | SPK 012 | SPK 019 | SPK 030 |
---|---|---|---|---|---|---|
Stroke [mm] | 35…400 | 40…400 | 65…400 | 80…400 | 70…400 | 90…400 |
Nominal force [lbs] | 450 | 900 | 1580 | 2700 | 4270 | 6745 |
Max. force [lbs] | 675 | 1350 | 2250 | 3370 | 4500 | 8990 |
Max. velocity [m/s] | 0.38 | 0.32 | 0.55 | 0.5 | 0.37 | 0.5 |
Force sensor/measurement | ||||||
Measurement technology | Strain Gauge | |||||
Measuring range [kN] | -0.3…+3 | -0.6…+6 | -1…+10 | -1…+15 | -1…+20 | -1…+40 |
Sampling rate [Hz] | 1000 | |||||
Resolution [bit] | 14 | |||||
Accuracy (linearity) [% FS] | +/- 3 | |||||
Servo drive (with integrated motion control) | ||||||
Power supply [V] | 1 x AC 110…230 3 x AC 110….230 | 1 x AC 110…230 3 x AC 110….230 | 3 x AC 200…500 | 3 x AC 200…500 | 3 x AC 200…500 | 3 x AC 200…500 |
Safety functions acc. to EN 61800-5-2 | Safe Torque Off (STO) 1) | |||||
Fieldbus interface | Profinet, Ethernet/IP, EtherCAT, Sercos III | |||||
Software functions | ||||||
Max. number of programs | 99 | |||||
Number of program steps per program | 500 | |||||
Number of digital inputs/outputs | 6 inputs + 1 output or 7 inputs | |||||
Force measurements | Unlimited without resolution reduction | |||||
Evaluation elements | Windows, envelopes, thresholds | |||||
Ambient conditions | ||||||
Ambient temperature (operation) [°C] | 0–50 °C (loss of performance at temperatures exceeding 40°C) | |||||
IP protection class | Mechanics: Standard IP54 (up to IP65 possible) Control cabinet hardware: IP20 |