Z – Standard In-Cylinder Rod Style
Analog
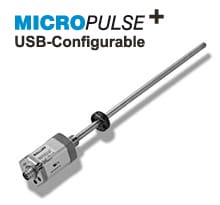
The Generation 7 analog rod-style transducer is available in two versions: the standard version is 100% backward compatible to previous Micropulse transducers, while the Micropulse Plus version offers an innovative USB interface for configuration and set-up.
- Linear displacement and/or velocity measurement (Plus version)
- M12/M16 connector or integrated cable
- 100% scalable analog outputs
- Status and set-up LEDs
- Two independent outputs (Plus version)
- PC-configurable (Plus version)
- 1″-300″ measurement length
- Output types: analog
- IP68 cable, IP67 connector
- Linear down to ±50 µm
- 150 g shock, 20 g vibration
- Enhanced electromagnetic immunity
SSI
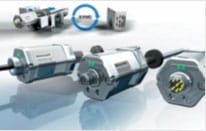
Benefits:
- Resistant to shock, vibration, and electrical interference
- Rod style pressure housing is rated to 8700 psi for use in high pressure hydraulic systems
- Stroke lengths to 300″ in 1″ increments
- Onboard bi-color LED’s for status and diagnostic indication
- Ingress protection up to IP68 assures dependable operation in extreme applications
Applications:
- High performance position feedback in closed-loop servohydraulic systems
- Steel processing machinery
- Sawmill equipment
- Metalforming
- Plastics and rubber manufacturing equipment
Digital
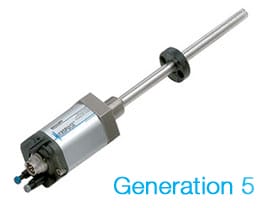
Pulse interface
The time between an interrogation and the reply signal is directly proportional to the position of the magnet along the waveguide. These pulses are transmitted using RS485/422 differential line drivers, guaranteeing noise-free signal transmission over distances of up to 500 m. The great advantage of these interfaces is the noise-immune signal transmission with a simple and economical interface. Interfaces with tristate outputs allow multiplexing of several Micropulse transducers. Appropriate control cards are available.
Quadrature
The quadrature output interfaces directly to standard encoder inputs (90° out of phase, A & B). This configuration gives you more interface options for connecting to motion based systems. In addition, the Micropulse quadrature output transducer has the ability to provide absolute position information through use of its innovative BURST function.
Fieldbus
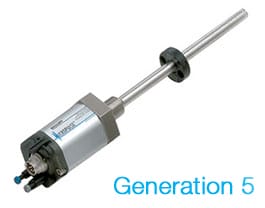
CANopen
The position of the magnet along the waveguide is sent over the CANbus to the controller in so called Process Data Objects or PDOs. Micropulse transducers work with standard CANopen protocols as per CIA DS 301 and with the standard device profile as per DS5406. CANopen offers greater flexibility because of the large number of configurations options for the transducer. For example, the resolution is programmable for 5, 10, 20 or 100 µm – depending on your application. Alternatively you can select whether both position and velocity information are sent to your controller, cyclically or on-demand. And there’s more: Up to 4 so-called software cams can be defined in the active measuring range. Each time the status of one of these cams changes, high-priority emergency messages are sent to the controller.
PROFIBUS
The Process Data Unit sends position and velocity information for the transducer to the controller via the PROFIBUS-DP. Micropulse transducers operate according to EN 50170 and support the PROFIBUS-DP encoder profile as well as multi-magnet operation. Micropulse transducers can be parameterized using the GSD file. The position resolution can be configured in 5 µm increments and the velocity resolution in increments of 0.1 mm/s. Working ranges and the null point can be configured individually for each magnet.