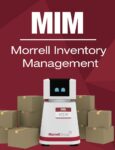
Do you spend valuable time managing fluctuating demand and supply chain disruptions? Even worse, do you find yourself still uncertain if your parts will arrive on time? Morrell Group has been handling these issues for our customers for years. We work closely with our customers to gain an understanding of their machines and their associated bill-of-materials (BOM), so we can schedule their parts for on-time delivery and manage any fluctuations in demand.
“Morrell ensures that, though I do not know which models I will be building 180 days from now, I will have the parts required to meet production goals by stocking levels of hydraulic components for all of the models and releasing according production requirements,” explains Bruce P., a rough terrain equipment manufacturer.
In addition to providing engineering and technical support, Morrell Group has been managing customers’ inventory unofficially for years. Now, we have formed an official program with established practices to continue to offer the same complimentary service to more mobile customers. Morrell Inventory Management (MIM) solidifies the process of streamlining your supply chain. You have a dedicated MIM team focused on managing changes in demand or lead times. You receive real-time updates and solutions to any potential supply chain disruptions. MIM allows you to stabilize your business and relax, knowing your parts will arrive on their scheduled delivery date.
“Morrell has always been ahead of the curve when it comes to scheduling and planning. By communicating effectively and innovatively anticipating our demand, Morrell helps provide us the flexibility to grow without fear of unanticipated spikes in demand from increased production, warranty, or field service needs. Their stocking and inventory programs ensure we always experience high levels of supply, and allow us the freedom to release just-in-time,” shared Lukas K., a forklift manufacturer.
OEMs can grow frustrated with long lead times, especially as they hold up machine production and deadlines are missed. With MIM, we manage long lead times with detailed forecasting and ongoing communication with our factory partners. Thanks to our longstanding vendor relationships, we are able to clearly communicate and push for delivery dates to keep your production lines moving. “Morrell is one of our favorite suppliers from a purchasing side because they manage the lead times of our products,” explained Ty H., an asphalt equipment manufacturer.
What if you need to build more machines than expected? No problem. Morrell Inventory Management is flexible, and our team will adjust accordingly. We can manage a sudden increase in business so you can fulfill all of your orders and your growth opportunities are not cut short. Your MIM team always plans for fluctuations in business based on your feedback, industry trends, and factory information.
MIM removes the uncertainty and inflexibility in your supply chain so you can optimize your equipment production. Inventory management does not have to be stressful. Partner with our team and experience a “sigh of relief.”
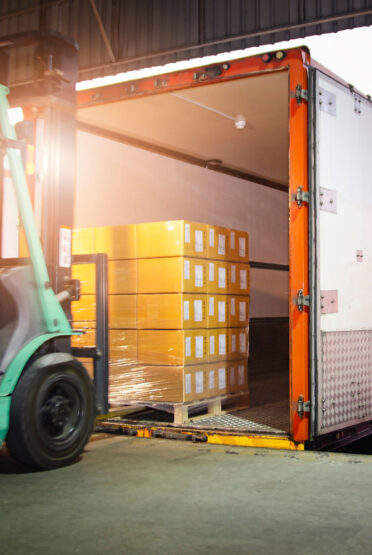