Discover how conveyor systems are tested and proven before shipment in part three of the Developing Automated Conveyor Systems series. Tim is joined by Kevin Curtis, Morrell Group’s Windsor Branch Manager, and Mason Cole, Senior Sales Engineer from Bosch Rexroth, to discuss the advantages of working with Morrell Group in developing Bosch Rexroth conveyor systems and their testing capabilities. Mason shares how customers regularly send their products to Bosch Rexroth’s Charlotte, North Carolina facility for testing on their VarioFlow model. He also shares insights on TS conveyor testing processes and how Bosch Rexroth ensures they are suitable for particular loads and applications.
TS conveyors have been in the field for 20+ years without issues. Mason shares how their modularity contributes to their longevity, especially in industries like automotive, where they are shifting from powertrain to battery manufacturing. The flexibility allows them to reuse many of the same parts and easily integrate new ones. Customers continue to request flexibility in their designs, as the products they are moving can rapidly change.
Learn what key features are proven in the VarioFlow testing process. While their North Carolina facility does not recreate an actual rendition of a conveyor system, they do test critical aspects to ensure viability. The team at Bosch Rexroth films the testing at various speeds to prove VarioFlow is a viable solution. Customers are also welcome to visit their North Carolina facility and attend the testing in person.
Mason shares examples of how testing has saved customers from challenges during implementation. For example, when testing small jars, they discovered an issue with shingling, which is when the product stops for accumulation and skews or tilts. By finding this during testing, they could implement a remedy before the customer integrated the conveyor and had to make adjustments on their factory floor.
Kevin shares the advantages of working with an engineering partner like Morrell Group, which provides value-added services and complementary products to complete your conveyor system. Kevin provides his experience with adding lubrication systems and sensors as examples. Morrell Group’s customers also experience the convenience of integrating a subassembly rather than receiving a “bag of bolts” to assemble themselves upon delivery. Discover the benefits of working with a dynamic team like Bosch Rexroth and Morrell Group in the final part of the Developing Automated Conveyor Systems Series on Evolution In Controls.
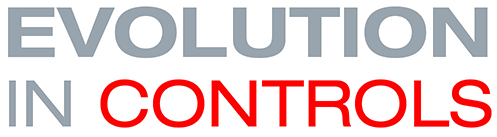